Today’s automotive industry is deeply reliant on steel, a material that accounts for roughly seven percent of global GHG emissions. On average, a vehicle contains about one ton of steel.
Steel is heavy and drags down efficiency. Lightweighting has already been a priority as the sector seeks to make internal combustion engine vehicles more efficient, but it’ll become all the more critical with the shift to EVs; EVs are heavier, on average, due to their weighty batteries.
The automotive industry is turning to aluminum for lightweighting, and for good reason: aluminum has a high strength-to-weight ratio—double that of steel—and is highly recyclable. While aluminum manufacturing from raw materials involves high energy-related GHG emissions, using recycled aluminum cuts the energy needed by 95 percent.
But today’s manufacturing techniques for fabricating aluminum parts—casting and 3D printing—can’t keep up with the speed or scale necessary to address the automotive industry’s voracious demand for aluminum. There’s 550 percent more aluminum in vehicles today than 50 years ago, according to the Aluminum Association, and the EV boom is just getting started.
Alloy Enterprises, a Greentown Labs startup, has developed a novel method for producing aluminum parts: selective diffusion bonding. This novel process creates parts layer-by-layer using laser-cutting, inhibiting, stacking, and diffusion-bonding (a type of welding).
Alloy Enterprises’ technology can produce aluminum parts quickly, cost-effectively, and at scale, all while delivering performance improvements through more complex shapes and stronger material properties.
“We have customers that report two-year lead times to get cast parts, and that’s just not the speed of innovation needed for electrification,” says Alloy Enterprises’ CEO and Co-founder Ali Forsyth. “Our value proposition is on-demand manufacturing at the unit cost of casting.”
Crucially, Alloy Enterprises doesn’t use aluminum powder, which is common in 3D printing today. By using aluminum sheets instead, the startup sidesteps 92 percent of the CO2 emissions associated with aluminum powder, according to Forsyth.
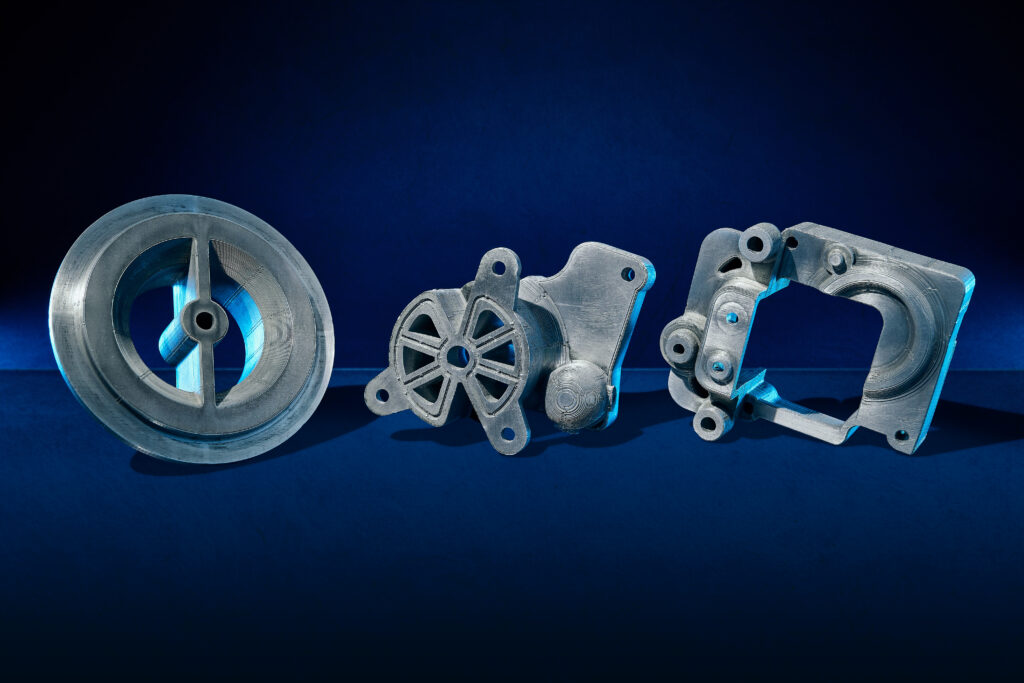
In addition to vehicles, Alloy Enterprises is also poised to manufacture parts for heavy and industrial equipment and the aerospace industry.
The startup announced an oversubscribed $26M Series A round last month, which will allow it to double its 25-person team by the end of 2023, reach pilot scale by the close of 2024, and more.
“Our seed investors both joined in this Series A round, and they originally found us through Greentown’s Investor Program,” Forsyth says. “I think very highly of that program, and it’s incredibly important for helping founders identify early funders.”
Alloy Enterprises has also secured its first 10 customers, according to Forsyth.
While Forsyth is a first-time founder, she’s no stranger to the startup journey—and no stranger to Greentown. An engineer by training, she’s worked at three Greentown member companies throughout her career. Forsyth and her co-founders, Nick Mykulowycz and Andie Bedell, started Alloy Enterprises in 2020.
“Greentown is really part of my story; I’ve woven in and through this community many times and been the lucky recipient of a lot of benefits,” Forsyth says. “When I think about how Greentown helps you build a company, what I keep coming back to is the fact that Greentown is an ecosystem and a community. People are helpful and supportive of their fellow founders.”